
There are quite a few important parameters of the frame that can now be adjusted by simply adjusting the measurements in variables at the top of the OpenSCAD source code.ĭo you want to build the tightest 2.5” HD micro quad? You can punch new measurements into two or three variables, and you can get the props as close to each other and the fuselage as you’d like. Getting the ratios and angles correct to make either extreme look right was challenging! The entire mount had to work well with the 9 mm hole spacing of an 1106 motor up to the 16 mm hole spacing of a 2207 motor. The diameter and spacing of those discs is based on the distance between the motor’s mounting holes. The mounts are built up using a configuration of hulls and fillets of a variety of discs. The most time-consuming task when creating the Kestrel was getting the guitar-shaped motor mounts right. Modeling in OpenSCAD requires more work up front, but it can pay off in the long run. You’ll start to get into the weeds when you try to model more organic shapes. OpenSCAD excels when you need to build objects that match precise measurements. If you’re a programmer, this may be easier for you to handle than a traditional CAD package. Everything is built from unions and differences of basic shapes like cubes, spheres, and cylinders. Instead of creating your objects by dragging and dropping various shapes and operations around the screen with your mouse, everything is defined using OpenSCAD’s programming language. It is nice to have an inexpensive "hold my beer" HD quad in my bag! /YW12ygHRIt- Pat Regan MaWhat can I do with the source code? The little warble my poor Kestrel has had on the pitch axis ever since upgrading the motors seems to be gone. I am much more excited about giving you the ability to cut your own frame than I am worried about someone selling copies of my design! All you need is the piece of the frame and a scanner.
#Cnc zacc fpv frames code#
I wish CNC machines were as readily available as 3D printers! If the source code is available, won’t that make it easier to clone the Kestrel?
#Cnc zacc fpv frames how to#
If I stop manufacturing frames, you could still acquire spare parts from someone else-I haven’t even figured out how to manufacture or sell these frames! If you have access to a CNC machine, you can cut your own. How does releasing an open-source frame help you? The most popular would be the TBS Source One frame.

There aren’t a lot of open-source FPV quadcopter frames to choose from.
#Cnc zacc fpv frames license#
Since I wanted to include that function in my source code, I had to license it under the GNU GPL 2 as well. I borrowed an awesome fillet function for OpenSCAD from Github, and that fillet function was licensed under the GNU GPL. I planned for the Kestrel to be open source from the beginning, but which license should I use? The choice of license was actually quite simple. The Kestrel is licensed under the GNU GPL 2
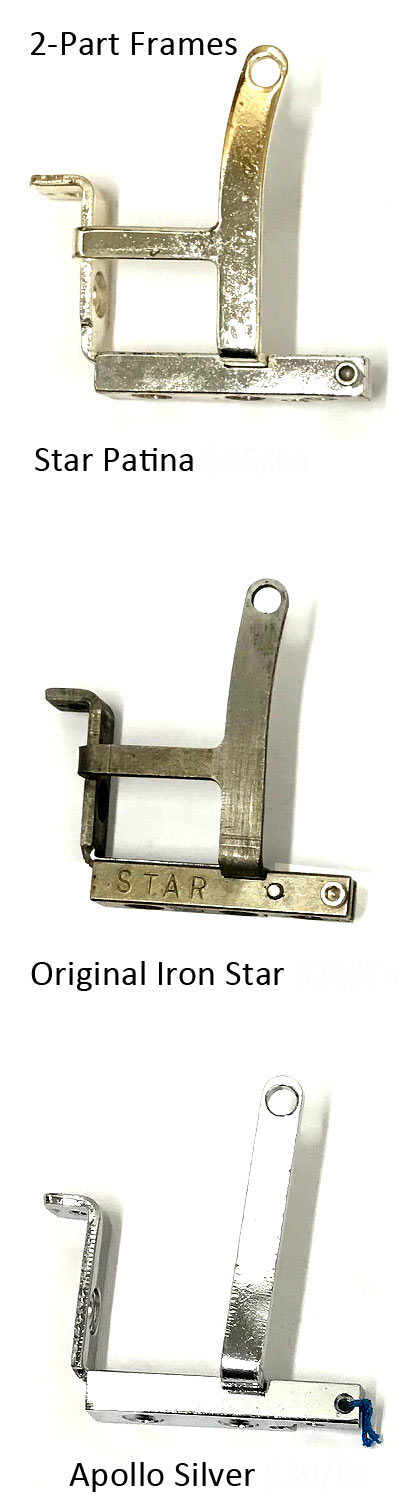
I usually get around 5 minutes of fairly aggressive freestyle out of it. NOT Included.My current build is using EMAX 1306 4000 kv motors, and it weighs 223 grams with a 650 mAh 4S pack. 2x 20x250mm Microfiber PU Leather Battery Strap (Color May Vary).IFlight Mach R5 5" Racing Carbon Fiber Frame Kit iFlight Beast F7 V1.2 45A AIO 25.5x25.5mm Flight Controller.Middle Plate thickness: 2.5mm CNC 7075 aluminum alloy.
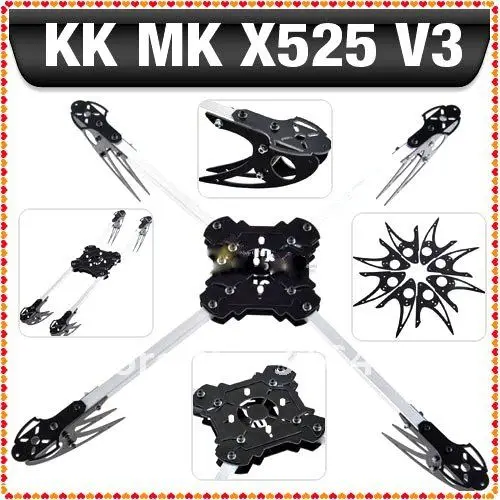
Super durable design, 6mm arms, and 7075 CNC middle plate VIDEO: Introducing Mach R5 - iFlight's First FPV RACE Drone the iFlight Mach R5 Frame Kit! iFlight's 5" Racing frame kit has quick-swap arm assembly and an enhanced canopy design with low wind resistance for maximum speed and efficiency.
